Custom Automation Design vs. Off-the-shelf Products — Which is Right for Your Facility?
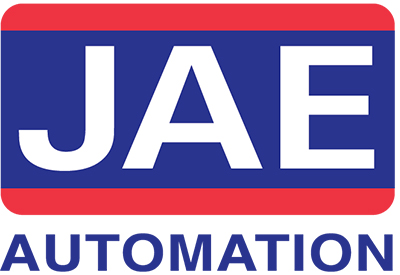
July 20, 2020
Eric Martin C.E.T., JAE Automation
The debate over whether to design a custom solution or purchase a commercial-off-the-shelf (COTS) product stretches back decades. And it’s not limited to the manufacturing sector. Across industries, the pendulum constantly swings from one side to another as companies seek out advantages and evaluate which approach is best suited for their business.
However, when it comes to automation technology, the answer, like many things in life, depends on the situation.
Each approach offers its own advantages and disadvantages, and the one that is best will depend on your unique requirements, specifications, and business strategy.
Understanding three approaches to automation technology
There are three distinct approaches that manufacturers can follow when implementing automation technology. The first is to purchase a COTS solution and install it as is, or with some light configuration and setup.
This approach works well if there is an existing solution in the market that meets your requirements. It’s often faster and more cost-effective to use an existing product, and it’s less risky as it’s already been proven in other manufacturing environments.
A stretch wrapper is a good example of a COTS solution. Stretch wrapping is fairly standardized and there are many vendors available, so choosing an off-the-shelf machine is likely appropriate in most cases.
That said, COTS solutions lack the flexibility, adaptability, and customization required for many of the more complex, unique, and emerging manufacturing processes. In these cases, a custom solution may be the best approach.
When designing and building a custom automation solution, manufacturers must factor in the additional time, budget, and uncertainty that comes with creating something from the ground up. Cost and schedule are less predictable, and there is a risk that the solution doesn’t work the first time.
But by going through the design process, manufacturers get a solution that meets their exact needs, specifications, and functionality. It’s possible to design entirely new ways of doing things and ensure that the new system fully integrates with both existing and future equipment.
And because the design company is less interested in commercializing the solution, in many cases manufacturers own the intellectual property. This is a significant advantage over a COTS solution if your process is proprietary and provides a competitive advantage.
Finally, it does not have to be an either/or decision. A hybrid approach that leverages off-the-shelf components or machines in a custom design may make the most sense. This allows companies to benefit from existing, proven, technology in a way that best aligns with their facility, process, and flow.
For example, an off-the-shelf box taper could be placed at the end of a custom conveyor system before the cases are put onto a pallet, stretch wrapped, and brought to the warehouse. From there, a fully integrated warehouse management software can track the location, batch number, and other relevant product information and send it to the company’s ERP system. This demonstrates how off-the-shelf components can be used in a custom system.
Asking the right questions when evaluating the right approach
There are a few basic questions you need to ask before diving in and making a decision.
What is our strategy and how will our facility look in the future?
Your strategy determines everything. From the requirements and specifications of your current project to the long-term direction of your manufacturing process and technology, a clear understanding of your strategy is critical before making any investment in automation. Together with your team identify why you’re investing in a new solution, what outcomes you expect to achieve, and how the change to your process will impact the rest of your facility.
Does a suitable COTS solution exist?
Once you’ve laid out your requirements and know how the new solution fits into your factory, you can determine if a suitable solution exists in the market. Knowing your requirements also allows you to accurately evaluate trade offs by making it clear what is a necessity and what could be left off if required.
Do we have budget and schedule flexibility?
As mentioned, a COTS approach offers more cost and schedule certainty, at least at the time of purchase. A custom solution, on the other hand, requires time and budget for design, building, testing, and implementation.
However, it’s also important to think about the total cost of ownership over the life of the equipment. Do you have the knowledge and expertise to configure an off-the-shelf solution, and what are the maintenance and repair requirements? What are the opportunity costs of implementing a solution that doesn’t quite meet your specifications, and would a custom solution generate a better return overall? These types of questions require a strong understanding of the true costs of your facility and of the competencies and skills of your team.
How does this integrate with existing and future systems?
Regardless of which approach you choose, the ability to integrate and communicate with existing and future systems should be a critical requirement of any solution. Some vendors have closed, proprietary systems that lock you in to their products, while others use open standards but require intensive integration effort on the part of the manufacturer. By considering not just what you have today, but also what you expect to implement going forward, you’ll be able to future-proof your new solution.
Choose the best approach for your unique situation
Some small and medium manufacturers are hesitant when it comes to custom automation design because they feel as though it’s only available to larger companies. However, a custom approach is well-suited to small and medium companies if it’s in line with the overall strategy and it addresses a specific business challenge.
With small changes, manufacturers can generate big returns and position themselves for future investments. By working with a trusted automation design partner, you’ll be able to identify which approach will generate the best return while helping you make things better.