Taking Pharma Quality Assurance to New Heights
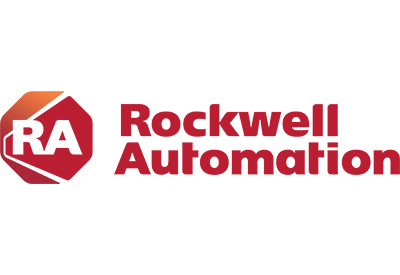
March 23, 2021
By Doan Chau, Technical Consultant, Life Sciences Industry
In the life sciences industry, quality is everything. But batch record review is a painstaking process if your company relies on exhaustive paper records – or a combination of paper and electronic records.
Large quality teams must comb through batch records to confirm good documentation practices (GDP) and initiate incident investigations when deviations are uncovered.
And because a myriad of issues can impact quality, following the paper trail to reach resolution can take weeks. Meanwhile, quarantined product waits for release, delaying availability to patients.
Today there’s a better way. An increasing number of life sciences companies are turning to manufacturing execution systems (MES) to reduce quality issues, accelerate resolution and improve operations.
Right from the Start
With MES software, you can create a holistic electronic batch record (EBR) that not only documents the process, but also guides each step to minimize quality issues at the onset.
We all know that following standard operating procedures (SOPs) is critical to maintaining product quality. But especially with manual operations, deviations from paper-based SOPs can easily occur despite the best intentions.
What happens when an operator misreads a barcode during a material addition step, enters an incorrect temperature setpoint, accidentally flips the page and moves on to the wrong step – or inadvertently uses uncalibrated equipment?
In some cases, the answer could be the loss of an entire batch.
An MES leverages the power of its EBR to add electronic guardrails that keep procedures on track – and reduce documentation and procedural errors by 50-80%.
How? Here are just a few examples. The MES can require barcode scans to electronically verify material additions and incorporate input limits to prevent inaccurate manual entries. The system shows your operators exactly where they are in the process – and only allows them to proceed per recipe design.
To enforce the use of the right equipment, the system could utilize barcode scans and access data from other systems to obtain maintenance, calibration and hygienic state data. Then, it electronically records the use in the electronic equipment logbook and EBR without the risk of manual data entry errors or omissions.
Accelerating Issue Resolution
Despite the guardrails provided by an MES, issues can occur. The cause might be as simple as an operator adding the incorrect amount of a substance during a manual addition. Or as complex as raw material variability reported by a supplier.
A robust MES helps you achieve resolution of these issues faster in two important ways.
First, the system enables “review by exception.” An EBR eliminates the time-intensive line-by-line confirmation of manual data entries. Instead, quality reviewers can focus on critical process exceptions – like an out-of-specification production reading that may directly affect the quality of the product.
The MES can identify these exceptions as they occur and report them to the right people via a dashboard to enable real-time correction and optimization.
Second, the system delivers complete genealogy and traceability. When a deviation does occur, the MES allows you to quickly identify all batches, lots and raw materials that were impacted. Root cause analysis investigation time can be reduced by as much as 30%, because the system tracks each step in the process – and all production-relevant resources including material, equipment and personnel.
Better Quality. Better Operations.
A holistic MES is designed to help you run and monitor your operations in real time. And it also provides richly contextualized data that’s ripe for analysis.
Because the system provides so much context around a specific batch including the product, materials and equipment used, even a manual analysis can quickly uncover insights into your process.
For example, MES data can show you how many deviations occurred in a specific time frame and which step of the process had the highest occurrence. This can lead to not only insights, but actions that can reduce impacts to quality – like adding electronic verification for a manual step or updating operator training.
Taking it a step further, analytics tools can help you correlate MES data with information from other systems. For example, adding data, such as temperature, humidity or particulate counts from your building management system, can help determine if environmental factors had an impact – guiding you to the root cause of the issue.
Extending Gains and Keeping It “Evergreen”
While an MES can significantly improve operations in a specific production facility, you can extend those gains by applying a common MES across your manufacturing footprint.
Oftentimes, a company’s production facilities have evolved over time – each in their own unique way. Some were established decades ago. Others are the product of mergers and acquisitions.
Regardless of the cause, the result is even plants within the same parent company can operate very independently.
An enterprise MES delivers a holistic view across all your production sites, leading to larger datasets, more robust insights – and more ways to make improvements. Because procedures and recipes can be shared, improvements identified at one site can be applied companywide.
And when you choose an MES that takes an “evergreen” approach to system upgrades, you can cost-effectively maintain your continuous improvement momentum.
Unlike many MES solutions, an evergreen MES allows you to incrementally upgrade the core functionality of your system, while preserving the master data and batch records of your sites. The result? Your system stays up-to-date without the cost of additional customization and new recipe validation.