4 Reasons You Need to Consider Robotics in Your Logistics Operations
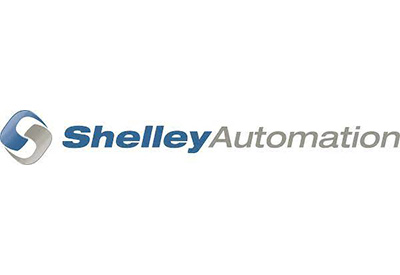
August 9, 2021
By Simab Khan, Marketing Specialist, Shelley Automation
Working alongside your current employees, Autonomous Mobile Robots (AMRs) can help improve your logistics operations. Here are four problems you may be facing and examples of how AMRs can help alleviate them.
1. Labour is hard to find, train, and retain
Given the current labor shortage in North America, it’s tricky to hire and retain enough permanent employees. And, during busy periods, hiring and training temporary workers is an additional challenge.
AMRs, like other robotics in logistics operations, can help you hire and retain staff. They make job openings more attractive to potential hires. And the robots can work alongside your existing staff, moving inventory to where people need it.
During busy periods, robots can work back-to-back shifts, day and night, so you can avoid the headache of hiring and training temporary staff.
Magna-Power is a manufacturer based in New Jersey. They improved the efficiency of their internal logistics operations by reducing the time employees spent moving materials between departments. The equivalent of three full-time employees that were freed from repetitive, low-value transportation tasks.
“The purpose of the robot is not to replace employees but to make them more efficient with their time. Now they can focus on the things that we can’t get a robot to do.” – Grant Pitel, Vice president of Engineering, Magna-Power.
2. Online shoppers have high expectations for fast, accurate orders
Canadians have been gradually doing more shopping online over the past few years. And e-commerce skyrocketed during the pandemic. Some experts predict this is a permanent change in shoppers’ behavior. Online customers expect accurate, fast orders. If your company falls short in accuracy and speed, you can lose out to competitors.
Automation in logistics can improve your company’s order accuracy and speed. Sometimes, robots are intrinsically faster than humans. But even when they’re slower, they don’t get distracted or bored and make mistakes like humans do. AMRs deliver the right products to the right place at the right time. Higher accuracy means that there’s less need for rework to correct mistakes. Less rework means faster orders. Fast and accurate orders mean happier customers (and fewer returns).
3. Warehouses can be unsafe environments for employees
Warehouses pose many risks for employees. As well as human safety, warehouse managers also need to consider the financial costs of these risks. The costs of insurance and time lost due to injuries (such as repetitive strains) and accidents (such as forklift-pedestrian collisions) can be considerable.
Warehouse automation with AMRs can make facilities safer for employees. For example, to replace a forklift in your warehouse, an AMR could be configured with a lifter module (with a payload up to 1000kg) to lift, transport, and deliver stacked pallets.
Other top modules — such as hooks, racks, and conveyors — can be attached to AMRs. The top modules are easy for employees to change so the same robot can be used for different tasks.
AMRs can even have cobot arms attached to them so they can move around the warehouse to pick and place products, reducing human repetitive motions and decreasing the risk of injury.
4. Inefficiency
Given the expense of labor — and the difficulty of hiring workers — you may be seeking to maximize the value of each employee and to ensure each one is working as efficiently as possible. If workers are spending a lot of each workday walking from place to place in your warehouse, or doing other mundane, low-value tasks, that is not the best use of your labor costs.
Using mobile robots for warehouse automation so employees spend less time transporting inventory means they can focus on higher-value tasks that are more strategic, creative, and collaborative.
Are AMRs a good fit for your logistics operations?
If you’d like to increase the efficiency, accuracy, and safety of your logistics operations, AMRs may be a good fit. Get in touch if you’d like to chat about how autonomous mobile robots might help in your warehouse.