Three Ways Today’s New Robotic Solutions Improve Logistics Applications
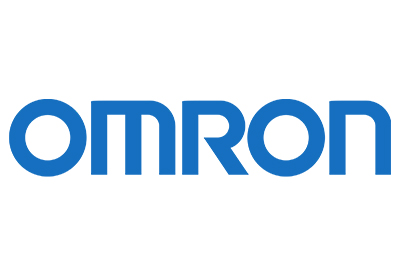
December 6, 2021
If you’re feeling like your employees are bogged down with repetitive tasks that are preventing them from using their creativity, you’re not alone in the logistics world. Many warehouses and distribution centers continue to rely heavily on manual activities like tote moving and order picking, which drain workers and sometimes lead to stress injuries.
Employees can make a greater contribution when they’re freed up from dull, unfulfilling tasks. Fortunately, today’s robotic solutions have advanced to the point where variations in product shapes and sizes are no longer an issue. This post will look at the potential contributions of collaborative robots (“cobots”) and autonomous mobile robots (AMRs).
Let’s examine three ways in which these next-generation technologies can make your logistics applications more efficient.
1. Robots speed up the process.
Great strides have been made in the development of collaborative robots that can work closely with people. Cobots provide versatile and scalable assistance to warehouse associates by automating repetitive tasks like palletizing. They also drive down costs by minimizing the possibility of human error.
Cobots are easy to integrate and have minimal impact on existing infrastructure (unlike industrial robots, which must be sequestered in cages due to safety concerns. In addition, cobots like Omron’s TM Series are simple to program, whereas industrial robots often require high levels of specialized expertise.
Autonomous mobile robots, like the LD series and HD 1500 series are also an excellent choice for speeding up processes in logistics operations where a person would be doing a lot of walking, such as “pick to order” operations. AMRs can serve as couriers that take items from the picking station to the pack-out locations, thereby reducing unnecessary travel throughout the warehouse (known as “motion waste”).
By automating manual tasks with cobots and AMRs, you can improve employee satisfaction and maintain output amid worker shortages. These robots can perform the boring and simple tasks while your employees focus on activities that use more creativity.
2. Robots maximize space utilization and flexibility.
If concerns about floor space are causing you to delay a transition to robotics, it may come as a surprise that many robotic solutions help maximize space usage. This is particularly true for autonomous mobile robots, which use onboard navigational software to move payloads through dynamic and peopled environments.
Because autonomous mobile robots allow for much more dynamic floor arrangements relative to conveyor systems, they fit easily into any floorplan. Thanks to their flexibility, they ensure easy re-deployment for any warehouse layout changes that can’t be made easily with fixed automation. The LD series AMR offers the the Mobile Planner software designed for viewing and controlling the a mobile fleet from a mobile device or tablet.
Assuming there’s enough physical space for AMRs to navigate through, they can adapt to almost any environment. The existing infrastructure can remain in place, or even be reduced (since AMRs can replace static conveyance systems). Special workflows can be quickly implemented simply by assigning a new route or task.
3. Robots improve safety.
Many logistics facilities rely heavily on forklifts. Although effective at moving pallets and other extremely heavy items, forklifts also pose safety concerns, particularly when operated by employees without special training. Many tasks normally executed by forklifts can be transitioned to AMRs, which can improve safety conditions.
AMRs have built-in safety rated laser scanners and are programmed with safety settings that prevent collisions with obstacles (including humans). As a result, the robots can operate in close proximity to human workers and other equipment with a much lower risk of injury or damage.